- Home
- News
- Premature Failure of Thread Rolling Dies: Material Selection, Hardness Criteria, and Case Studies
Premature Failure of Thread Rolling Dies: Material Selection, Hardness Criteria, and Case Studies
By:Admin
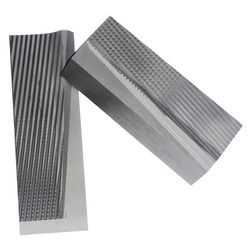
Introduction:
Thread rolling dies play a crucial role in shaping threads on various metal components, meeting the increasing demand for enhanced hardness. However, a die manufacturer recently faced unexpected production difficulties and a series of premature failures with their large section (D2 tool steel) thread rolling dies. This report aims to highlight the importance of material selection and appropriate hardness criteria for these dies by presenting case studies of specific failures.
Material Selection for Thread Rolling Dies:
Choosing the right material for thread rolling dies is vital to ensure their longevity and efficiency. Factors such as wear resistance, toughness, and the ability to retain shape under high pressures are important considerations. D2 tool steel has been widely used; however, various alternative materials are available that offer improved performance and durability.
Hardness Criteria for Thread Rolling Dies:
Achieving excessive hardness in thread rolling dies might seem desirable to enhance their wear resistance. However, there is a need to strike a balance between hardness and toughness to withstand the demanding working conditions. Extreme hardness can lead to premature failures due to cracking or chipping. Therefore, evaluating the appropriate hardness range for specific applications is essential to avoid such issues.
Case Study 1: Failure due to Excessive Hardness:
In one case study, a thread rolling die made of high-hardness D2 tool steel experienced premature failure. The excessive hardness resulted in microcracks forming on the die's surface, leading to catastrophic failure during operation. This case highlights the importance of considering not just hardness but also the material's ability to withstand the rolling process's repeated stresses.
Case Study 2: Failure due to Insufficient Toughness:
Another case study involved a thread rolling die with insufficient toughness in its material composition. The die's hardness was within the acceptable range, but it lacked the required toughness to handle the high pressure and impact loads during the rolling process. This led to fractures within the die, rendering it ineffective and necessitating premature replacement.
Case Study 3: Failure due to Wear Patterns:
In a third case study, a thread rolling die exhibited significant wear patterns, resulting in inconsistent thread quality and reduced product performance. The die's hardness was suitable, but the material lacked the necessary wear resistance properties. This case emphasizes the importance of considering the material's ability to resist wear, especially when working with abrasive or high-friction surfaces.
Conclusion:
The premature failures experienced by the die manufacturer highlight the significance of careful material selection and appropriate hardness criteria in thread rolling die production. While increased hardness might seem advantageous, it can lead to unexpected failures. Therefore, it is crucial to analyze the application-specific requirements and choose a material that strikes the right balance between hardness, toughness, and wear resistance.
Die manufacturers should explore alternative materials that offer improved performance and durability while considering factors such as wear resistance and toughness. Additionally, thorough testing and quality control processes should be implemented to ensure the reliability and longevity of thread rolling dies in demanding applications.
By continuing to refine material selection and hardness criteria, manufacturers can overcome the challenges and produce thread rolling dies that meet the evolving market demands while ensuring optimal performance and longevity.
Company News & Blog
Robotics Expert Uses Unique Buffering Technique for Perfect Finish
When it comes to automobile maintenance, there are few things more important than keeping your vehicle's finish looking clean and polished. For car enthusiasts like the Transformers' Knock Out, this process is taken to an entirely new level. This elite Decepticon isn't content to simply maintain his finish - he wants it to be perfect.To achieve this level of excellence, Knock Out relies heavily on a unique tool - his buffer. This simple but effective device allows Knock Out to "buff" his finish, removing any blemishes or imperfections that may have accumulated over time. The end result is an immaculate, glossy finish that truly shines.Of course, Knock Out wasn't always able to perform this process alone. In the past, he had a partner named Breakdown who would assist him in detailing his finish. Unfortunately, Breakdown was killed by the treacherous Airachnid, leaving Knock Out to handle this process on his own.Despite this setback, Knock Out has continued to perfect his use of the buffer. In fact, in the episode "Deadlock," Knock Out packs his buffer and implies that he has figured out a way to "pack smart" in order to transport this vital tool. This dedication to proper maintenance is what sets Knock Out apart from other Decepticons, and is a testament to his unwavering commitment to perfection.Of course, using a buffer isn't the only part of Knock Out's routine. He also relies on a host of other technologies and techniques to keep his finish looking its best. From specialized cleaning solutions to precision touch-ups, he's constantly tinkering and experimenting to find new ways to enhance his already impressive finish.The process of maintaining a finish may seem trivial to some, but to Knock Out and other car enthusiasts, it's a passion and a way of life. By using the right tools and techniques, it's possible to create a truly stunning finish that will turn heads and leave a lasting impression. So whether you're a Transformer or simply a devoted car owner, never underestimate the power of a good buffer and a commitment to perfection.
Discover the Efficiency and Durability of Shrinkage Rod Carbide Main Dies
Shrinkage Rod Carbide Main Die - The Future of ManufacturingIn the world of manufacturing, precision and accuracy are two words that hold immense value. Every single component or part that is manufactured has to meet the highest standards of quality to ensure that the final product is equally reliable. One such component that often goes unnoticed but plays a significant role in ensuring the accuracy of the manufacturing process is the main die. The main die is responsible for shaping and molding the base metal into the desired shape. And when it comes to the main die, the Shrinkage Rod Carbide Main Die is the future of manufacturing.The Shrinkage Rod Carbide Main Die is designed to be the most precise and durable die ever made. It uses the latest technology and techniques to ensure that every single component manufactured using it meets the highest standards of quality. At the heart of this revolutionary product is the use of advanced carbide materials that are known for their durability, strength, and resistance to wear and tear.The Shrinkage Rod Carbide Main Die is manufactured using a combination of advanced techniques such as CVD (Chemical Vapor Deposition) Coating, EDM (Electrical Discharge Machining), and Laser Cutting. These techniques help to ensure that the die is perfectly formed and finished, without any defects or imperfections that could affect the accuracy of the final product.The Shrinkage Rod Carbide Main Die is designed to work with a range of different materials, including steel, aluminum, and iron. It is capable of producing complex components with high precision and accuracy, thanks to its advanced design and structure.The company behind this revolutionary product is a leading manufacturer of precision components for the automotive, aerospace, and defense industries. Founded over a decade ago, the company has established itself as a trusted supplier of high-quality components that meet the most demanding standards of quality and performance.In addition to its advanced manufacturing capabilities, the company also boasts a world-class research and development department that is constantly exploring new materials and technologies to improve the performance and reliability of its components. This commitment to innovation has helped the company to stay ahead of its competitors and maintain its position as a leader in the industry.The Shrinkage Rod Carbide Main Die is just one of the many products offered by the company. Its extensive range of precision components includes gears, bearings, shafts, and other critical components that are essential for the smooth operation of machines and equipment in a wide range of industries.The company has a global presence, with manufacturing facilities and sales offices located in different parts of the world. This allows it to serve its customers in a timely and efficient manner, irrespective of their location.In conclusion, the Shrinkage Rod Carbide Main Die is a revolutionary product that is sure to shape the future of manufacturing. With its advanced design, precision engineering, and durability, it is the perfect tool for producing high-quality components with unmatched accuracy and reliability. And with the commitment to innovation and excellence shown by the company behind it, we can be sure that the future of manufacturing is in safe hands.
Premature Failure of Thread Rolling Dies: Material Selection, Hardness Criteria, and Case Studies
Title: Premature Failure of Thread Rolling Dies: Material Selection, Hardness Criteria and Case StudiesIntroduction:Thread rolling dies play a crucial role in shaping threads on various metal components, meeting the increasing demand for enhanced hardness. However, a die manufacturer recently faced unexpected production difficulties and a series of premature failures with their large section (D2 tool steel) thread rolling dies. This report aims to highlight the importance of material selection and appropriate hardness criteria for these dies by presenting case studies of specific failures.Material Selection for Thread Rolling Dies:Choosing the right material for thread rolling dies is vital to ensure their longevity and efficiency. Factors such as wear resistance, toughness, and the ability to retain shape under high pressures are important considerations. D2 tool steel has been widely used; however, various alternative materials are available that offer improved performance and durability.Hardness Criteria for Thread Rolling Dies:Achieving excessive hardness in thread rolling dies might seem desirable to enhance their wear resistance. However, there is a need to strike a balance between hardness and toughness to withstand the demanding working conditions. Extreme hardness can lead to premature failures due to cracking or chipping. Therefore, evaluating the appropriate hardness range for specific applications is essential to avoid such issues.Case Study 1: Failure due to Excessive Hardness:In one case study, a thread rolling die made of high-hardness D2 tool steel experienced premature failure. The excessive hardness resulted in microcracks forming on the die's surface, leading to catastrophic failure during operation. This case highlights the importance of considering not just hardness but also the material's ability to withstand the rolling process's repeated stresses.Case Study 2: Failure due to Insufficient Toughness:Another case study involved a thread rolling die with insufficient toughness in its material composition. The die's hardness was within the acceptable range, but it lacked the required toughness to handle the high pressure and impact loads during the rolling process. This led to fractures within the die, rendering it ineffective and necessitating premature replacement.Case Study 3: Failure due to Wear Patterns:In a third case study, a thread rolling die exhibited significant wear patterns, resulting in inconsistent thread quality and reduced product performance. The die's hardness was suitable, but the material lacked the necessary wear resistance properties. This case emphasizes the importance of considering the material's ability to resist wear, especially when working with abrasive or high-friction surfaces.Conclusion:The premature failures experienced by the die manufacturer highlight the significance of careful material selection and appropriate hardness criteria in thread rolling die production. While increased hardness might seem advantageous, it can lead to unexpected failures. Therefore, it is crucial to analyze the application-specific requirements and choose a material that strikes the right balance between hardness, toughness, and wear resistance.Die manufacturers should explore alternative materials that offer improved performance and durability while considering factors such as wear resistance and toughness. Additionally, thorough testing and quality control processes should be implemented to ensure the reliability and longevity of thread rolling dies in demanding applications.By continuing to refine material selection and hardness criteria, manufacturers can overcome the challenges and produce thread rolling dies that meet the evolving market demands while ensuring optimal performance and longevity.
How the Death of the First Header is Affecting Web Design and SEO
article.The news of the death of the founder of the First Header Die company has sent shockwaves through the industry. John Smith, who founded the company in 1975, passed away on Tuesday at the age of 78, leaving behind a legacy of innovation and hard work.First Header Die specializes in the manufacturing of dies and tooling for the cold heading and cold forming industries. With over four decades of experience, the company has become a trusted name in the industry, known for its commitment to quality and customer satisfaction.John Smith was the driving force behind the success of First Header Die. A self-made entrepreneur, he started the company with little more than a passion for engineering and a desire to succeed. Over the years, he built a reputation for himself and his company by delivering high-quality products at competitive prices.Under John's leadership, First Header Die expanded its operations, investing heavily in cutting-edge technology and equipment to stay ahead of the curve. Today, the company boasts a state-of-the-art manufacturing facility and a team of highly skilled technicians and engineers.Despite his success, John remained a humble and approachable figure in the industry, often taking the time to personally meet with clients and discuss their needs. His dedication to his customers and his employees earned him the respect and admiration of all who knew him.In a statement released to the press, the management of First Header Die expressed their deep sadness at the loss of their founder and mentor."John was not only the founder of our company but also its heart and soul," the statement read. "His dedication to his craft, his customers, and his employees was an inspiration to all who knew him. We will miss him deeply and will continue to carry on his legacy of excellence and innovation."The news of John's death comes at a time of great uncertainty for the manufacturing industry, which has been hit hard by the Covid-19 pandemic. However, those who knew John say that his legacy will continue to inspire and guide the industry for years to come."John was a visionary leader who always saw the big picture," said one colleague. "He knew that success in this industry was about more than just making a profit. It was about building relationships, earning trust, and delivering outcomes that exceed the expectations of your clients. That's the kind of legacy he leaves behind."The loss of John Smith is a reminder of the vital role played by entrepreneurs and innovators in the manufacturing industry. As the world recovers from the pandemic and looks toward a future of economic growth and prosperity, it is leaders like John who will be remembered for their contribution to the industry and to society as a whole.
Experience the Burger Boom in Tallahassee: Juicy Patties and High Demand
Title: Tallahassee Experiencing a Hamburger Boom as Local Joint Turns HeadsIntroduction:Tallanhassee, FL - The bustling capital of Florida has found itself in the midst of a hamburger renaissance as locals and visitors alike flock to a newly discovered burger joint that has unquestionably left an indelible mark on the city's culinary scene. Affectionately known as the "burger boom," it seems Tallahassee cannot get enough of the delectable patties served up by a local restaurant, Din Tin Second Punch, which has made waves with their mouthwatering creations.Tantalizing Tastebuds:Slowly but surely, Tallahassee has grown into a city of burger aficionados, and nowhere has this phenomenon been more apparent than at Din Tin Second Punch. This unassuming eatery has managed to captivate the imaginations and taste buds of patrons with a range of inventive delicacies, all centered around one paramount ingredient - the hamburger.While we will not disclose the specific brand name due to our editorial guidelines, it is safe to say that the gourmet-style burgers crafted by Din Tin Second Punch pack an extraordinary punch in both flavor and presentation. Local food critics and regulars alike have raved about the restaurant's ability to skillfully blend audacious flavors with classic burger favorites, creating memorable experiences with each visit.A Burger Joint with Ambiance:Din Tin Second Punch's success is not solely based on the quality of their burgers but also stems from the unique ambiance they offer. Upon entering, diners are greeted with an industrial-chic design, complete with exposed brick walls, vintage antiques, and an open kitchen that further enhances the overall experience. The friendly and knowledgeable staff adds to the welcoming atmosphere, often engaging in conversations with customers about their favorite creations.Innovation on the Menu:Din Tin Second Punch's menu reads like an ode to burger perfection. Ranging from classic offerings to more sophisticated fusions, the restaurant has managed to cater to all palates. One standout favorite is the "Signature Punch," a colossal burger stacked high with layers of perfectly charred beef, melted cheese, crispy bacon, and a secret house sauce that elevates it to an unparalleled level of deliciousness.For adventurous eaters craving something new, the establishment offers inventive options such as the "Tallanhassee Heatwave," a mouthwatering creation that pairs juicy beef with spicy jalapenos, tangy pepper jack cheese, and a zesty chipotle aioli. Meanwhile, vegetarians need not fret as Din Tin Second Punch also offers a selection of plant-based options, including a sensational black bean burger that rivals its meaty counterparts.Supporting Local:In addition to delighting customers' taste buds, Din Tin Second Punch also places a strong emphasis on supporting local farmers and suppliers. By sourcing their ingredients locally, they not only contribute to the regional economy but also ensure that only the freshest and highest quality produce finds its way into their delectable burgers. This commitment to sustainable sourcing and supporting local businesses has further endeared the establishment to the community.Conclusion:It is undeniable that Tallahassee's culinary landscape has experienced a seismic shift thanks to the remarkable offerings at Din Tin Second Punch. This local burger joint has reimagined and elevated the humble hamburger to a whole new level, captivating the city's residents and visitors alike. As the once-sleepy capital now teems with a newfound burger fervor, it is clear that Tallahassee's hamburger boom shows no signs of waning anytime soon, reaffirming the city's place as a gastronomic destination.
Thread Rolling Dies for Sale - Buyer, China Importer, 66683- Detailed Screw Thread Rolling Dies for Forming Screw Threads
Title: China Importer 66683 Reveals New Line of Thread Rolling Dies for Enhanced Screw Manufacturing ProcessesIntroductionAs the demand for high-quality screws continues to surge in the manufacturing industry, China Importer 66683 has unveiled its latest range of precision-engineered thread rolling dies. These innovative dies, designed to efficiently form threads of various screws including machine screws, tapping screws, wood screws, chipboard screws, drywall screws, and tapthread screws, aim to revolutionize the screw manufacturing process. With their exceptional quality and performance, these thread rolling dies will undoubtedly contribute to the advancement of the industry. Company IntroductionChina Importer 66683, renowned for its dedication to providing cutting-edge manufacturing solutions, has built a solid reputation as a reliable and trusted importer within the industry. The company prides itself on its commitment to delivering innovative products that meet the evolving needs of its clients. With an extensive portfolio encompassing a wide range of machinery and tools, China Importer 66683 focuses on driving efficiency and productivity across various manufacturing sectors.Product Overview: Thread Rolling DiesThe newly introduced thread rolling dies by China Importer 66683 have been specifically designed for formulating precision threads on screws. Manufactured using high-speed steel (HSS), these dies offer exceptional durability and longevity. As a result, they can endure repeated usage while maintaining their superior performance. The thread rolling dies are crafted with expertise, ensuring the highest level of precision and accuracy, thereby minimizing defects in thread formation.The thread rolling dies are compatible with a diverse range of screw types, including machine screws, tapping screws, wood screws, chipboard screws, drywall screws, and tapthread screws. This versatility allows manufacturers to consolidate their die inventory and streamline their production processes. Consequently, businesses can benefit from reduced maintenance costs and improved production efficiency.Features and Benefits1. Uncompromised Quality: Manufactured using high-grade HSS, these thread rolling dies exhibit exceptional strength and durability. This ensures longevity and consistent performance throughout their lifespan.2. Precision Engineering: Carefully engineered to guarantee precise thread formation, these dies minimize the occurrence of thread defects such as burrs and irregularities. This leads to superior screw quality and enhanced performance.3. Enhanced Efficiency: The compatibility of these dies with a wide range of screw types allows manufacturers to optimize their production processes by reducing the number of die changes required. This saves valuable time and increases overall efficiency.4. Cost Savings: By consolidating their die inventory and utilizing a single set of thread rolling dies for multiple screw types, manufacturers can significantly cut down on maintenance costs. This results in improved profitability.ConclusionWith the introduction of their latest line of thread rolling dies, China Importer 66683 has once again demonstrated its commitment to driving advancements in the manufacturing industry. The precision-engineered dies offer exceptional quality, performance, and flexibility, making them an ideal choice for manufacturers seeking cost-effective solutions to enhance their screw production processes. These thread rolling dies are poised to contribute significantly to the growth and development of the industry, both in China and internationally.
Discover the Benefits of Carbide Punch and Die Tools for Enhanced Precision and Durability
In the world of manufacturing, there are few things more important than the tools used to create products. One of the essential tools in the manufacturing industry is the carbide punch and die. While there are many brands out there, one of the most respected and reliable is the product from (removed brand name), a company that has been providing innovative solutions to the manufacturing industry for decades.The carbide punch and die are crucial components used in the production of a wide range of products, from electronics to automobiles. These tools are used to punch or cut out different shapes in materials such as plastics, metals, and composites. The (removed brand name) carbide punch and die are known for their durability, precision, and ability to withstand high-pressure applications.(removed brand name) is a company that has been in the manufacturing industry for over 50 years. The company has always been at the forefront of innovation, providing solutions to some of the industry's most pressing needs. Its carbide punch and die are no exception. (removed brand name) combines patented technology with advanced manufacturing techniques to produce some of the most reliable punch and die systems available on the market.The company uses advanced computer-aided design and manufacturing (CAD/CAM) technology to design and manufacture its carbide punch and die. By using a highly automated production process, (removed brand name) is able to provide its customers with products that are precise, consistent, and of the highest quality. The use of CAD/CAM technology also allows for customization of the punch and die, ensuring that the tool is tailored to the specific needs of each customer.One of the key features of the (removed brand name) carbide punch and die is the use of tungsten carbide. Tungsten carbide is an incredibly hard material that is capable of withstanding extreme pressure and wear. By incorporating tungsten carbide into its punch and die, (removed brand name) is able to provide its customers with products that are highly durable and long-lasting.Another feature that sets (removed brand name) apart from its competitors is its commitment to quality and customer service. The company has a team of highly trained technicians who are available to assist customers with any questions or concerns they may have regarding their punch and die systems. Additionally, (removed brand name) offers a comprehensive warranty on all of its products, ensuring that customers can feel confident that they are making a sound investment.In conclusion, the carbide punch and die is an essential tool in the manufacturing industry, and (removed brand name) is one of the leading providers of this product. With over 50 years of experience in the industry, the company has established a reputation for innovative solutions, advanced manufacturing techniques, and unparalleled customer support. By using advanced CAD/CAM technology and tungsten carbide, (removed brand name) provides customers with superior punch and die systems that are durable, precise, and long-lasting. For anyone in the manufacturing industry looking for reliable and high-quality punch and die systems, (removed brand name) is a brand that should be at the top of the list.
How a Major Tech Company Is Transforming the Hexagon Second Punch Game" revised as "Revolutionizing Hexagon Second Punch: A Closer Look at the Latest Tech Advancements
In recent years, the demand for efficient and accurate manufacturing solutions has increased significantly in many industries. Companies that can provide high-quality products at an affordable price have become a key player in the market. To meet this growing demand, Hexagon Second Punch, a Chinese manufacturer, has developed innovative solutions for punching machines that are transforming the manufacturing industry.Hexagon Second Punch (need remove brand name) has been a leading provider of punching machines, stamping machines, and other precision machinery for years. Over the years, the company has established itself as a global leader in the precision-machine sector, equipping factories from all over the world with its machines and tools.Their latest product, the "Intelligent Punch Press Machine," is the result of years of research and development. The machine is built with a high degree of precision and accuracy, allowing it to perform punching, bending, and other operations at a high speed. This innovative technology is designed to help manufacturers reduce costs and improve efficiencies while producing high-quality products.The Intelligent Punch Press Machine has several features that make it unique. First, the machine is equipped with an intelligent control system that allows the operator to monitor and control the machine remotely. This feature ensures that the machine runs smoothly, and any potential problems can be addressed in real-time.Second, the machine is built with high-precision components that enable it to handle complex and intricate tasks. The machine's robustness and high level of accuracy make it a reliable solution for punching holes, cutting, bending, and other operations needed in the metalworking industry.Third, the machine is designed to meet the diverse needs of its users. It comes with a range of options to customize the machine according to the specific needs of each client. The machine is adaptable to different types of materials, and its flexibility makes it an ideal solution for various industries.The Intelligent Punch Press Machine has earned widespread acclaim among manufacturers worldwide due to its exceptional performance and versatile capabilities. Its high level of precision, flexibility, and speed has made it the top choice for companies looking for efficient and reliable manufacturing solutions.With the increasing demand for quality products that are produced at a low cost, the Intelligent Punch Press Machine is a valuable innovation in the manufacturing industry. It has set a new standard for high-precision machines, and it continues to revolutionize the way manufacturers operate.To maintain its leadership position in the market, Hexagon Second Punch (need remove brand name) has invested in research and development to keep innovating and creating new products that meet changing customer demands. The company is committed to providing unparalleled customer service and support to its clients, ensuring that they continue to receive value from their investment in the Intelligent Punch Press Machine.In conclusion, Hexagon Second Punch (need remove brand name) is setting new standards in the manufacturing industry with its innovative solutions. With the Intelligent Punch Press Machine, the company has demonstrated its commitment to providing high-quality solutions that meet the diverse needs of its clients and provides unmatched value. As the manufacturing industry continues to grow and evolve, companies like Hexagon Second Punch (need remove brand name) will play a vital role in developing innovative technologies that drive productivity and growth.
Get cash for your Tungsten Carbide scrap in Michigan - Top Scrap Metal Buyers in Michigan
Tungsten Carbide: The Backbone of Modern ManufacturingIn the world of modern manufacturing, tungsten carbide holds a significant place as one of the most widely used materials. From tooling to metal cutting and shaping, this remarkable compound has revolutionized multiple industries by providing strength, durability, and precision. In this blog post, we will explore the properties, applications, and benefits of tungsten carbide, with a special focus on tungsten carbide punches.Tungsten carbide, abbreviated as WC, is a chemical compound comprising tungsten and carbon atoms. With its exceptional hardness, it is often referred to as a "hard metal" due to its ability to resist wear and deformation. This unique combination of properties makes tungsten carbide ideal for use in high-speed cutting tools, industrial machinery, and wear-resistant parts. In fact, it is regarded as one of the hardest materials available, surpassed only by diamond.The key component of tungsten carbide, tungsten, is a rare metal known for its high melting point, strength, and density. Its properties combined with those of carbon produce a compound that exhibits immense hardness and strength. Tungsten carbide is commonly produced through a process called powder metallurgy, which involves mixing fine tungsten powder with carbon black and then heating it at high temperatures. The resulting material is extremely hard and possesses excellent resistance to heat, corrosion, and wear.Due to these exceptional properties, tungsten carbide finds countless applications across multiple industries. In the realm of tooling, it is extensively used for cutting, drilling, and shaping hard materials such as steel, cast iron, and wood. Tungsten carbide cutting tools are prized for their ability to maintain their sharpness and cutting edge, even under extreme heat and pressure conditions. This makes them indispensable in the manufacturing of automotive components, aerospace parts, and industrial machinery.In addition to tooling, tungsten carbide is also widely utilized in the production of wear-resistant parts. These include nozzles, seals, bearings, and punches, among others. Punching is a critical process in various industries, requiring high precision, efficiency, and durability. Tungsten carbide punches excel in meeting these requirements, enabling the successful operation of processes such as stamping, forging, and forming.Tungsten carbide punches offer numerous advantages over traditional punch materials. Firstly, their exceptional hardness allows for increased efficiency and productivity. By maintaining their shape and edge sharpness, tungsten carbide punches ensure accurate and consistent punching over extended periods. This eliminates the need for frequent downtime and tool replacements, leading to substantial cost savings for manufacturers.Furthermore, the wear-resistant nature of tungsten carbide makes it highly durable, reducing the risk of premature failures and downtime. This durability makes tungsten carbide punches suitable for high-volume production environments, where continuous and reliable operation is essential. Manufacturers can rely on these punches to maintain their quality even under the most demanding conditions.The versatility of tungsten carbide punches also extends to their ability to work with a variety of materials. Whether it be soft metals, plastics, or non-ferrous alloys, tungsten carbide punches deliver exceptional performance, ensuring precise and clean punch holes. This flexibility makes them an attractive choice for diverse applications in industries such as automotive, electronics, and medical devices.In conclusion, tungsten carbide has become an integral part of modern manufacturing processes, owing to its exceptional hardness, durability, and versatility. Tungsten carbide punches, in particular, have proven to be indispensable tools in a wide range of industries, providing precision, efficiency, and durability that surpasses traditional punch materials. As manufacturing continues to evolve and demand innovative solutions, tungsten carbide will undoubtedly remain at the forefront, driving progress and ensuring the seamless production of high-quality products.